Por Marcelo Carugo, VP Industry Programs and Alliances, Emerson Automation Solutions
La Administración de Información de Energía de EE. UU. proyecta que las emisiones de dióxido de carbono (CO2) irán disminuyendo hasta el 2050 en los países de la Organización para la Cooperación y el Desarrollo Económicos (OCDE), que incluye a EE. UU.1 Esta proyección asume que el consumo de energía irá aumentando hasta el 2050, y que los productores cumplirán estas demandas con una combinación de fuentes de energía tradicionales y renovables. Los sitios de pozos y las refinerías pueden contribuir a estas reducciones de emisiones proyectadas siguiendo las prácticas recomendadas descritas en este artículo.
Impulsar una mayor eficiencia: Cualquier instalación que se proponga aumentar la eficiencia debe tener sus operaciones en orden en todos los frentes. Esto significa que la producción debe controlarse de manera efectiva con una operación estable, con un equipo bien mantenido y seguro. Si hay problemas operativos en estas áreas, la gerencia debe solucionarlos primero, ya que los costos e incidentes relacionados pueden tener efectos negativos mucho mayores en comparación con las reducciones en el consumo de energía.
Este artículo examinará tres áreas en las que las instalaciones pueden mejorar la eficiencia energética al utilizar tecnologías disponibles en la actualidad:
- Sistema de información para la gestión energética (EMIS)
- Sistema de monitoreo predictivo de emisiones (PEMS)
- Gestión energética y caudal másico
Según los proyectos en los que los ingenieros de la empresa del autor han trabajado en una variedad de refinerías, las mejoras pueden sumar hasta un 2 % o un 3 % del costo correspondiente. Dadas las cantidades que una refinería típica gasta en energía, estas cifras se traducen en números muy grandes, y cualquier reducción resulta en aumentos sustanciales en la rentabilidad, junto con las correspondientes mejoras en la sostenibilidad.
EMIS: Comprender el consumo de energía: La medición es un primer paso crítico para la gestión energética porque muchas instalaciones no saben lo suficiente sobre cómo están consumiendo la energía como para reducirla. Obviamente, la instalación tiene una cantidad agregada, pero es posible que no pueda determinar el volumen asociado con una unidad individual o un calentador de fuego específico. Analicemos esta situación y veamos cómo abordar este problema.
Los costos de energía en una refinería típica se encuentran entre los costos operativos más altos, si no el más alto, a menudo hasta el 50 % de los costos de refinación. El costo total comprende numerosos factores relacionados con los tipos de combustible disponibles, costos de combustible individuales, eficiencia del equipo (calderas, calentadores de combustible, etc.), condiciones de operación y una variedad de otros factores. Para complicar aún más las cosas, en una refinería promedio, alrededor del 41 % de la energía simplemente se pierde.
¿Se puede arreglar esta situación? Sí, sin duda. Esta es la realidad: el cuartil superior de las empresas de la industria tiene menos de la mitad de la intensidad energética del cuarto cuartil. Piense en lo que eso significa. Las mejores refinerías consumen la mitad de energía por volumen de producción que las peores. ¿Cómo lo hacen esas mejores empresas?
Primero, miden el consumo de energía (FIG. 1) de forma granular en tiempo real. Es posible ver cuánto y qué tipo de combustible está consumiendo un calentador, una caldera u otro equipo encendido en cualquier momento. Esta capacidad requiere instrumentación y las redes que la respalden, con avances en sensores inalámbricos que simplifican la implementación y reducen los costos. A menudo, esto incluye agregar instrumentación a los equipos que actualmente no se monitorean de manera integral o no se monitorean en absoluto.
En segundo lugar, toda la instrumentación crea grandes cantidades de datos que deben capturarse e historiarse. Hay muchas plataformas capaces de proporcionar visualización; sin embargo, algunas instalaciones se detienen aquí, como si la captura de datos fuera un fin en sí mismo. Dichos programas no brindan los resultados deseados, lo que requiere avanzar al siguiente paso.
Tercero, los datos deben ser analizados. Aquí es donde las instalaciones se dan cuenta de las verdaderas diferencias en metodología y eficacia. Una plataforma analítica básica debe cubrir, al menos, las siguientes cinco acciones:
- Valide los sensores para garantizar mediciones precisas sin ruidos ni valores defectuosos.
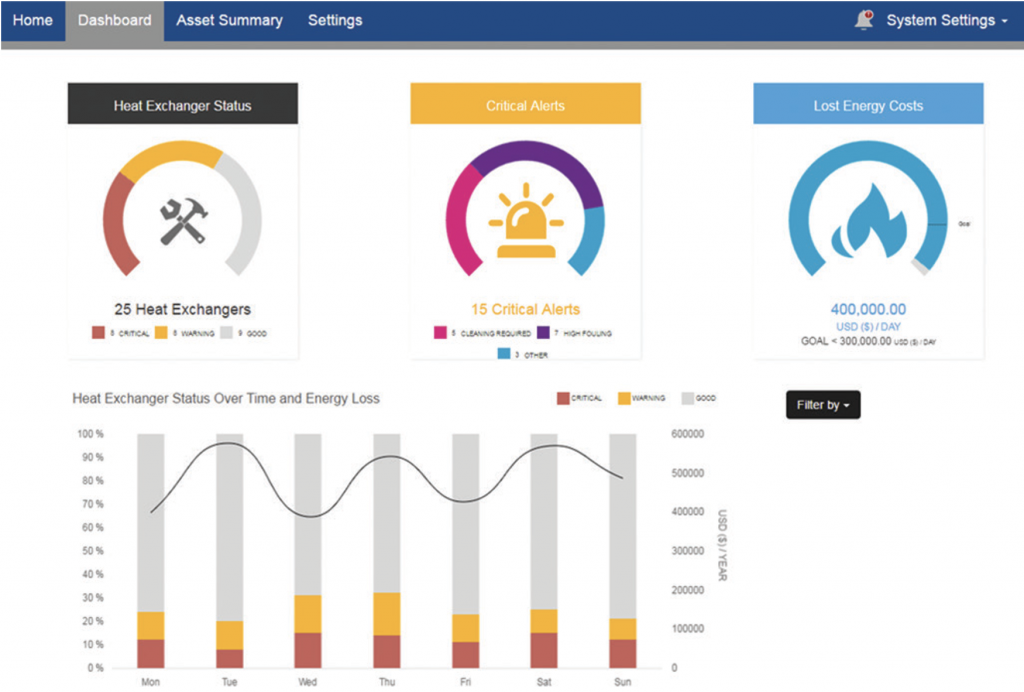
FIG. 1. Los tableros pueden mostrar el consumo de energía, incluida la energía desperdiciada, en tiempo real
2. Monitoree los indicadores clave de desempeño (KPI), al mostrar datos en paneles de usuario e identificar áreas problemáticas.
3. Ajuste los objetivos dinámicos en función de los estados de la planta y los modos de operación, al mismo tiempo que identifica situaciones anormales y posibles alteraciones del proceso.
4. Aísle las causas principales detrás de las brechas de desempeño y proporcione acciones correctivas sugeridas.
5. Calcule puntos de ajuste para optimizar el consumo de energía en múltiples niveles operativos y minimizar así el costo.
La medida en que una plataforma dada realiza estas funciones es el principal vaticinador del éxito general del proyecto. Por ejemplo, los modelos predictivos adjuntos a objetivos dinámicos pueden ir más allá de la simple identificación de situaciones anormales. Un sistema realmente sofisticado no solo debe rastrear estas situaciones en tiempo real, sino también ofrecer un análisis de lo que está fallando en el proceso (FIG. 2). De esta forma, el modelo puede profundizar en las interacciones y ofrecer formas prácticas de mejorar la operación, más allá del ahorro de energía.
Saudi Aramco y EMIS: Como un breve ejemplo, Saudi Aramco lanzó un proyecto EMIS en su instalación de Abqaiq, la planta de procesamiento de petróleo y estabilización de crudo más grande de su flota. El EMIS instalado cubre 24 unidades de producción, 57 unidades de no producción y 237 equipos críticos. La gerencia de la empresa quería mejorar el consumo de energía promedio anual de la instalación de 30,000 Btus/bbl del equivalente de petróleo. Además de muchas preocupaciones comunes a la mayoría de las refinerías, esta instalación también tenía problemas específicos que resolver, entre ellos:
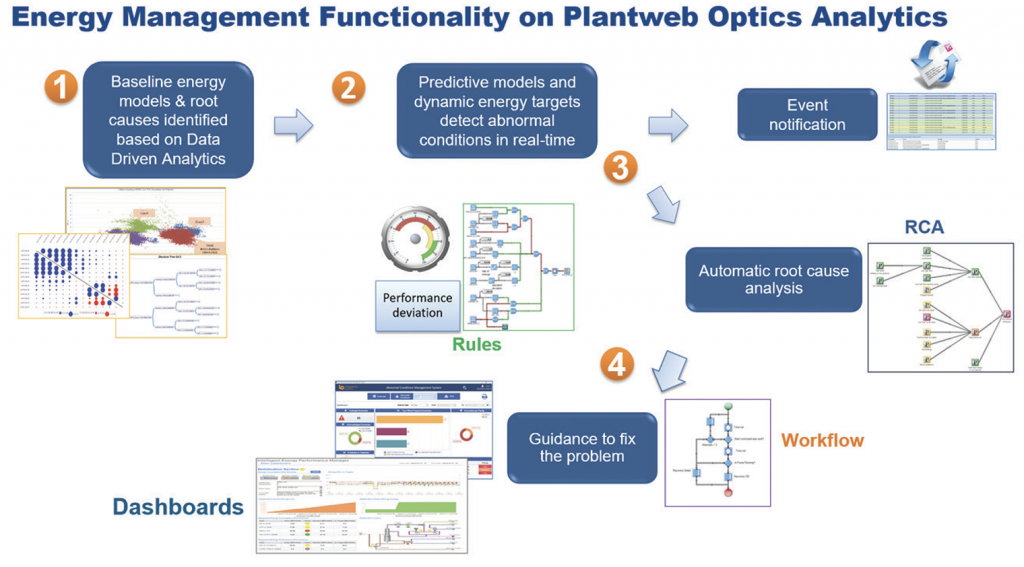
FIG. 2. Un sistema eficaz no solo informa datos, sino que ofrece sugerencias sobre cómo los operadores pueden mejorar las operaciones
- Los sistemas de monitoreo de energía existentes informaron muchas advertencias falsas de consumo excesivo que eran difíciles de solucionar.
- En ocasiones, los operadores se encontraban operando con objetivos incorrectos debido a cambios en el modo de la planta y los estados impulsados por un cambio a un crudo diferente.
- Los operadores estaban ajustando cargas y alimentaciones sin suficiente información para considerar los impactos completos en el desempeño de cada unidad y su equipo
Los ingenieros que diseñaron el EMIS capturaron los datos correctos para analizar y resolver las preocupaciones operativas básicas, pero también las exclusivas de cada unidad. Estos datos se combinaron con tableros (FIG. 3) configurados para mostrar variables críticas, de modo que los operadores pudieran mantener un conocimiento crítico de la situación de las operaciones del proceso y del consumo de energía y luego tomar las medidas apropiadas.
Estas acciones se basaron en 13 modelos de optimización, cada uno de los cuales utilizó problemas de programación no lineal y métodos de problemas de programación no lineal de enteros mixtos para entregar resultados que minimizaran el consumo de energía en todas las plantas.
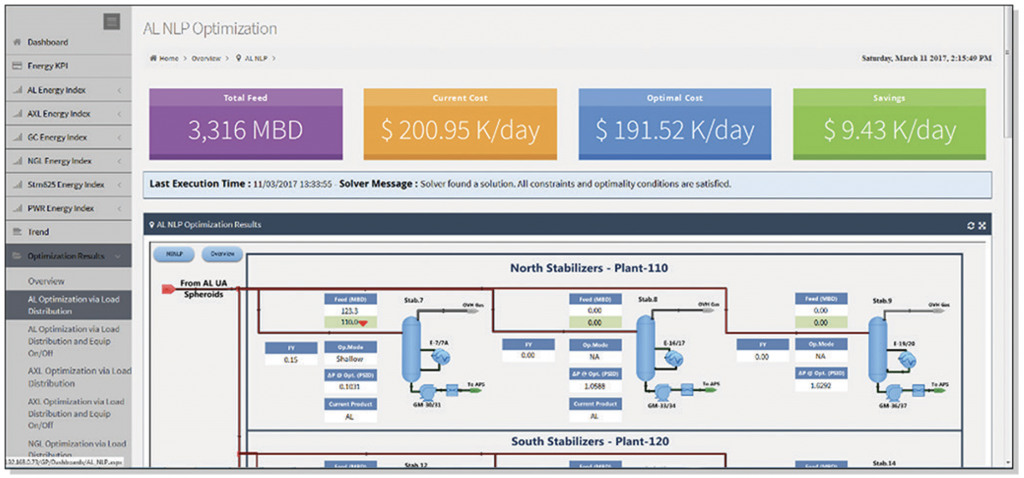
Los resultados del proyecto incluyeron:
- Un ahorro estimado en costos de energía de $22 MM en el primer año.
- Una mayor visibilidad del desempeño operativo para los operadores y la gestión mejoró la toma de decisiones en todos los niveles.
- Tiempo del ciclo para la resolución del problema más rápido.
- Los mejores puntos de ajuste y parámetros clave para la mayor rentabilidad retenida y compartida entre los operadores.
PEMS: Ampliación de las capacidades de la gestión energética: Muchos procesos de combustión dentro de una refinería están regulados por la Agencia de Protección Ambiental de EE. UU. (EPA) o su equivalente en otros países. Tales agencias requieren que la mayoría de los calentadores, calderas y equipos similares tengan un sistema de monitoreo continuo de emisiones (CEMS) para medir y registrar la salida de varios contaminantes del aire cada vez que el equipo está en funcionamiento. Los contaminantes en este contexto pueden incluir dióxido de azufre, óxidos de nitrógeno, monóxido de carbono, CO2, amoniaco, oxígeno y posiblemente otros. La solución convencional en estos casos es implementar una y potencialmente más tecnologías de analizadores de gases diseñadas para cuantificar los contaminantes relevantes para cada fuente.
Este enfoque puede funcionar bien cuando se aplica correctamente; sin embargo, puede volverse complejo y costoso, particularmente cuando una instalación dada puede quemar múltiples tipos de combustibles capaces de producir diferentes efluentes. Si existe la oportunidad de ahorrar dinero al usar un combustible económico durante algún tiempo, pero el analizador no puede manejar los efluentes probables, es una oportunidad perdida. Además, dada la cantidad de aplicaciones probables en una refinería, puede haber docenas y tal vez cientos de instalaciones de analizadores, todas las cuales requieren calibración, consumibles (gases especializados) y mantenimiento apropiados.
En muchos aspectos, el mayor inconveniente de este enfoque es lo poco que ayuda a mejorar el proceso o a reducir los costos. Los analizadores CEMS están ahí con el único propósito de monitorear las emisiones. Si los operadores en la sala de control pueden ver lo que están informando, lo que no suele ser el caso, es posible que obtengan una indicación de que algo anda mal con la combustión, pero esto no siempre es muy útil.
Una mejor alternativa es usar un PEMS basado en datos en lugar de un CEMS convencional. El PEMS crea un modelo (FIG. 4) del proceso de combustión con los datos de EMIS, historiadores, sistemas de gestión de activos u otras bases de datos de procesos.
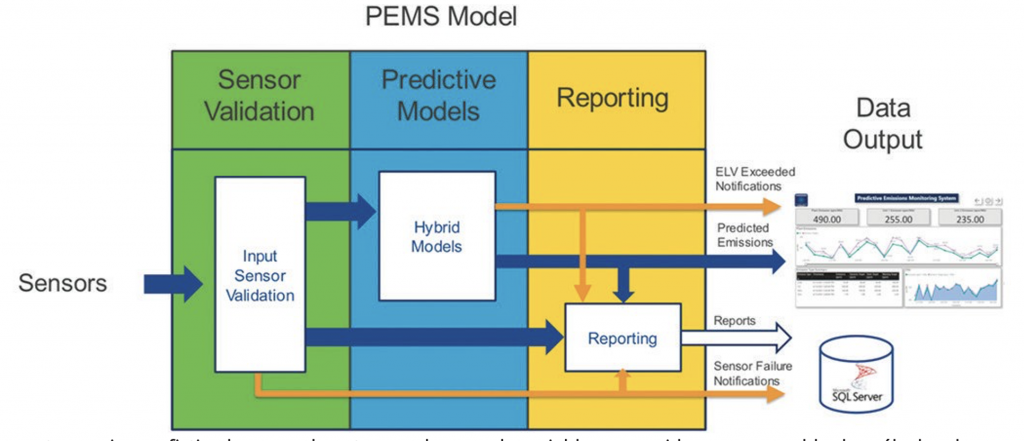
FIG. 4. Un PEMS utiliza un modelo de proceso para determinar la salida de contaminantes de un calentador o caldera encendidos
Dado que el PEMS monitorea todos los factores relevantes, como el flujo de combustible, el flujo de aire, el tipo de combustible, etc., puede calcular la salida de efluentes en tiempo real basándose en un modelo de combustión sofisticado. El modelo dice, en efecto, dado este conjunto de parámetros operativos, aquí está el perfil de los efluentes.
Esta metodología se describe en las reglamentaciones pertinentes, incluida la EPA CFR 40 de EE. UU., Parte 60-61-63-75 y en la Unión Europea bajo CEN/TS 17198:2018. El organismo regulador insistirá en evaluar una determinada instalación para asegurarse de que el proceso se realiza correctamente. Normalmente, la certificación de una instalación requiere una serie de pasos:
- Verificar que la aplicación sea adecuada para PEMS
- Validar sensores para precisión y confiabilidad
- Evaluar la integridad del modelo de emisión
- Revisar documentación y capacitación
Una vez que se superan estas pruebas y el sistema está instalado y en funcionamiento, la aplicación debe probarse y validarse periódicamente. Algunos de estos serán controles internos, pero la agencia reguladora participará, al menos, anualmente con su propia prueba de vigilancia.
El uso de un PEMS ahorra dinero en comparación con un CEMS tradicional (FIG. 5) al considerar tanto el costo de capital como el costo operativo de por vida, especialmente cuando se incluye el mantenimiento y los consumibles para los analizadores convencionales. Sin embargo, tan importante como el costo, un PEMS puede funcionar en conjunto con el EMIS porque es parte del EMIS más grande.
Por lo tanto, proporciona información sobre el proceso de maneras que no son prácticas con un CEMS. También puede ser parte de estrategias de optimización de procesos más grandes y esfuerzos de eficiencia energética.
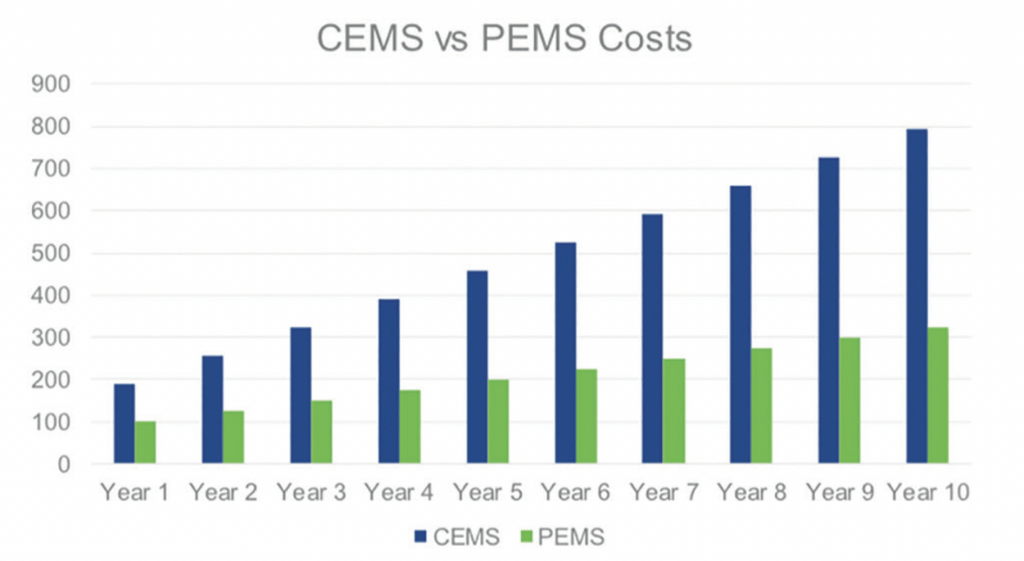
FIG. 5. Un PEMS es mucho menos costoso y mucho más versátil que un CEMS
Balance de masa: Producción para el aporte de energía: La pregunta que todos los gerentes de refinerías deberían hacerse es, ¿cuánto producto obtenemos por cada unidad de energía? Este es un cálculo muy importante, pero es muy complejo ya que hay muchas variables. El panorama general también incluye las capacidades y limitaciones básicas de una unidad de producción en función de las conversiones, los rendimientos, la selectividad del catalizador, los puntos de corte del fraccionador y la eficiencia energética.
Un EMIS puede proporcionar el lado energético de la ecuación, que es otro beneficio de dicho sistema, pero para muchas instalaciones, el eslabón débil de examinar en el balance de masa resultan ser mediciones precisas de los flujos de productos en puntos críticos del proceso. El punto crítico es medir el caudal másico, pero en muchas instalaciones, la instrumentación de caudal solo mide el volumen. Esto es un problema porque las mediciones de volumen no tienen en cuenta la densidad del producto, lo que puede provocar errores de cálculo.
Los siguientes son varios ejemplos típicos de problemas:
- Dado que la densidad no se mide, se supone que es constante, usando el mismo valor en todas las situaciones para un producto dado.
- El procesamiento de lotes de crudos de oportunidad provoca cambios en las características de la materia prima, que pueden reconocerse con una lectura de caudal másico real, pero pueden pasar desapercibidos si se supone que la densidad es constante.
- Si es necesaria una lectura de densidad crítica, algunas instalaciones usan análisis de laboratorio de muestras al azar; sin embargo, esto no rastrea las condiciones cambiantes.
- La conversión de volumen a masa para flujos de alta temperatura es problemática, ya que las tablas del factor de corrección de volumen del American Petroleum Institute se detienen en 400 °F (200 °C).
- Es posible implementar instrumentos de densidad en el campo, pero existen limitaciones de temperatura y productos viscosos.
- Dado que la masa no se mide con precisión, la optimización de procesos por medio de estrategias avanzadas de control de procesos no es práctica.
Pasar a la medición de caudal másico: Podría decirse que la mejor tecnología de caudalímetros para aplicaciones de refinería es Coriolis (FIG. 6). Estos caudalímetros no solo miden el caudal másico de forma nativa, sino que también miden la densidad directamente en tiempo real y tienen compensación de temperatura interna. La mayoría de los diseños incluyen un transmisor sofisticado capaz de entregar el rango de variables requeridas para respaldar los cálculos de balance de masa. Además, son muy precisos en un amplio rango de temperaturas y rangeabilidad.
Su desventaja es el costo relativamente alto en comparación con las tecnologías de medición alternativas, junto con un pequeño paso libre interno en comparación con el tamaño de la línea. Donde los flujos de productos no son limpios, pueden ser propensos a obstrucciones, particularmente con tamaños de línea pequeños. Sin embargo, si bien el costo es una consideración, el precio de compra más alto es mucho menor que los ahorros realizados por las plantas que los instalan en puntos críticos. Incluso una ligera mejora en la producción puede pagar el caudalímetro en semanas o meses.
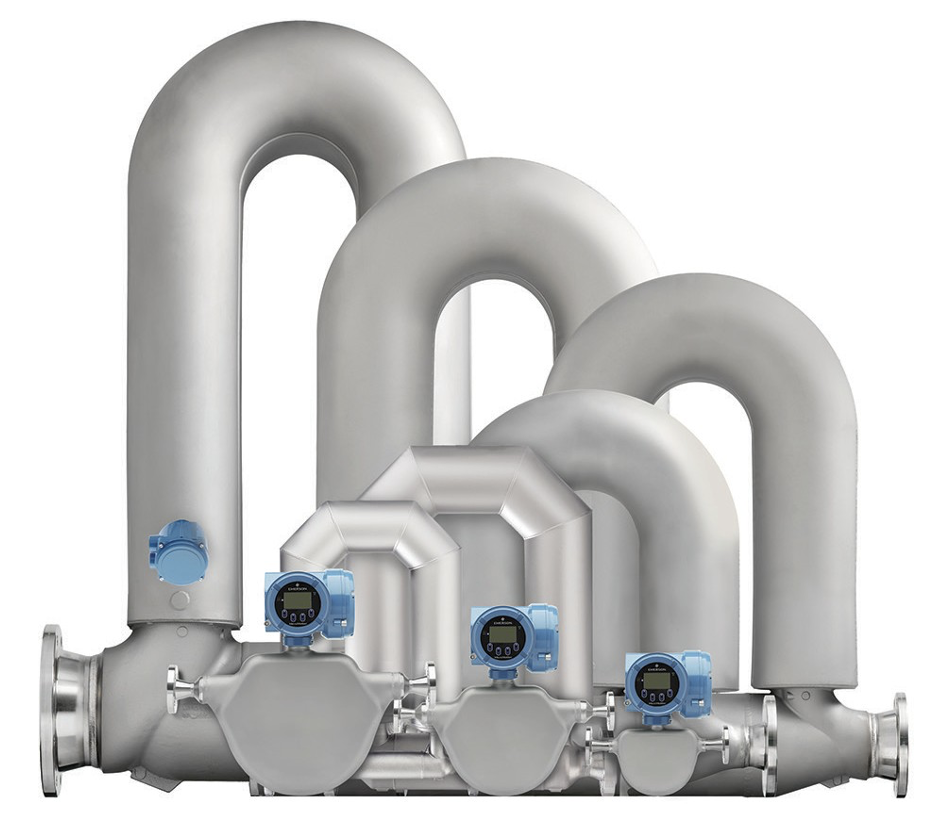
FIG. 6. La tecnología Coriolis suele ser la mejor opción para las lecturas de caudal másico real utilizadas para los cálculos de balance de masa
Una configuración de caudalímetro más común en las refinerías es la presión diferencial (dP). Esta tecnología funciona bien en todo tipo de instalaciones, pero no puede proporcionar una medición de caudal másico sin conocer la densidad del producto. Si la densidad es relativamente constante, el transmisor o el sistema host de automatización pueden usar el valor de densidad, con el ajuste apropiado para la temperatura y calcular el caudal másico. Esto funciona solo cuando hay una lectura de temperatura en el caudalímetro, que puede ser parte de ese medidor o de una capturada cerca.
Para las instalaciones y unidades de producción donde hay una gran base instalada de caudalímetros de dP, es probable que haya una combinación de instalaciones confiables y problemáticas. La mayoría de las instalaciones de dP se pueden mejorar al verificar algunas consideraciones básicas de operación y mantenimiento, que incluyen lo siguiente:
- ¿Cuántos años tiene el transmisor? Los transmisores de dP de hoy en día tienen capacidades que no estaban necesariamente disponibles hace solo unos años. Esta actualización económica puede agregar nuevas funciones multivariables a una instalación existente.
- ¿Las líneas de impulso son fáciles de mantener? Las líneas de impulso mal diseñadas pueden tener filtraciones u obstruirse, lo que interfiere con las mediciones precisas. Cuando los sedimentos son un problema, se pueden configurar para una fácil limpieza.
- ¿Cuál es la condición de la placa de orificio? Los usuarios deben verificar que los bordes del orificio aún estén afilados, que el orificio esté centrado y que no se haya agrandado debido al desgaste. Se puede hacer una verificación con un micrómetro para verificar que no haya perdido área superficial, lo que cambiaría la relación beta.
- ¿La instalación tiene suficiente tubería recta?
Para lograr una precisión total, los caudalímetros de dP necesitan secciones de tubería rectas aguas arriba y aguas abajo de la placa de orificio. Verifique que todas las instalaciones tengan la longitud requerida. ¿Cuándo se calibró el transmisor por última vez? Realice las acciones de calibración necesarias y verifique que el rango siga siendo apropiado para la aplicación.
Beneficios obtenidos de los esfuerzos en el balance de masa: Los esfuerzos diseñados para mejorar el balance de masa siguiendo los métodos discutidos pueden brindar mejoras importantes a las refinerías. Los siguientes son tres breves ejemplos:
- Con su sistema de medición existente, una refinería no pudo cumplir con el objetivo de ±2 % en su unidad de destilación al vacío/destilación de crudo. Usaba caudalímetros de dP y un caudalímetro ultrasónico. Reemplazó 10 de las instalaciones de dP con caudalímetros Coriolis, y luego pudo llevar la unidad rápida y consistentemente dentro de un objetivo de ± 1 %.
- Una refinería en el este de Europa no podía exceder el 96 % de cierre del balance de masa usando caudalímetros de dP, a pesar de que habían sido muy exigentes con el mantenimiento y la calibración. Reemplazaron nueve de las mediciones más críticas con caudalímetros Coriolis. No solo redujeron el tiempo dedicado al mantenimiento, sino que también pudieron mejorar el balance de masa al 99,4 %.
- Otra refinería tuvo problemas para estabilizar su unidad de hidrocraqueo debido a la variabilidad de la materia prima. Al utilizar caudalímetros de dP convencionales, los operadores no pudieron compensar con precisión los cambios de composición. Al colocar un caudalímetro Coriolis en la línea principal de la materia prima, los operadores pudieron reconocer los cambios en la materia prima, lo que les permitió alcanzar
sus objetivos de producción y monitorear la desactivación del catalizador. Un aumento del 2 % en el rendimiento valió $1 MM en el primer año.
Uniendo todo: Un proyecto eficaz de sostenibilidad por medio de la eficiencia tiene muchos aspectos; por lo tanto, requiere coordinación para lograr las metas deseadas. Cada elemento puede generar ganancias de forma individual, pero cuando se vinculan entre sí a través de un plan maestro común (FIG. 7), los efectos verdaderamente sinérgicos pueden multiplicar los beneficios. La gerencia debe considerar este tipo de plan como una clave para los avances a largo plazo capaces de mejorar las ganancias, reducir la huella de carbono y hacer que las operaciones sean más sostenibles.
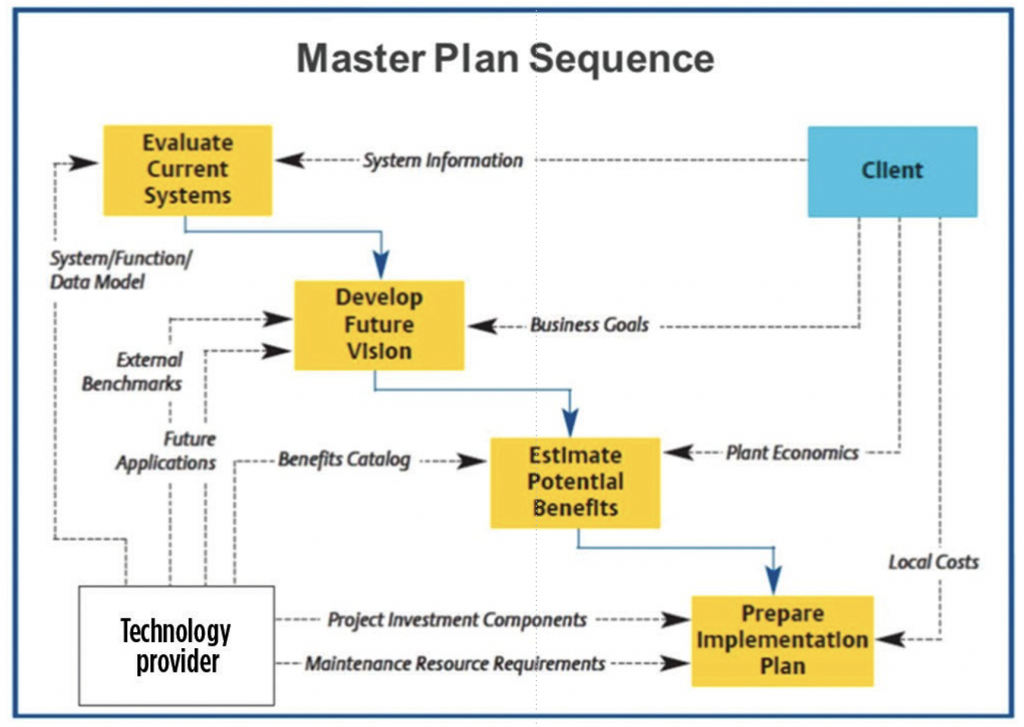
FIG. 7. Un plan maestro une todos los elementos de un proyecto de eficiencia para maximizar los beneficios totales